Samsung display QD-OLED yield exceeded 85% and then increase production, how to follow the domestic printing OLED?
Time: Oct 22, 2022Views:
Recent news from the supply chain shows that Samsung Display's QD-OLED TV panel yield has broken through to 85% from the original 70% to 80%, signaling that Samsung Display's QD-OLED TV panel will likely enter the profitability stage. The panel industry generally takes 85% yield as the capacity break-even line to set the factory price of panels.
At the same time, Samsung Display is further optimizing the process parameters of the production line by speeding up the production beat to increase the capacity from 30,000 sheets per month now to 40,000 sheets next year. It is very common in the panel industry to increase production by reducing the beat time, including LGD's plant in Guangzhou, where the same method was used to significantly increase the monthly production of panels from 60,000 to 90,000. Currently Samsung display for the production of QD-OLED panel Q1 production line, its 8.5 generation of glass substrate monthly output of 30,000 pieces.
In terms of product categories, starting next year Samsung Display will start producing QD-OLED panels in larger sizes of 77" and 49". QD-OLED panels will cover 34", 49", 55", 65" and 77".
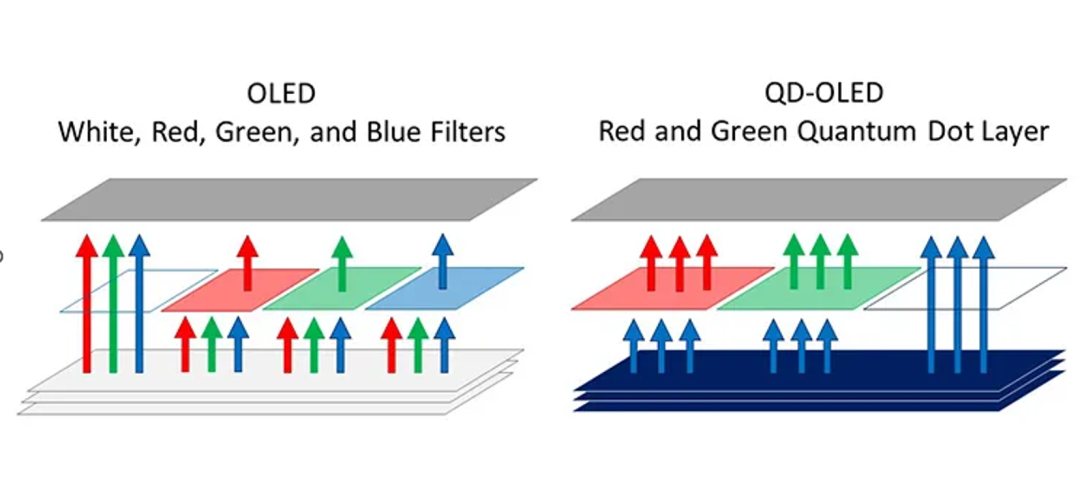
Unlike conventional W white OLED + color RGB OLED TV panels, Samsung Display's QD-OLED panels provide red and green by using blue as the base OLED color as the base layer, and then using quantum dot (QD) layers in the sub-pixels. Since blue has the shortest wavelength in the primary color, the QD layer converts blue to red or green by absorbing some energy to form the new pixel color.
Since QD-OLED panels are self-luminous RGB tri-color mixing systems, they lose less luminance than traditional filter panels and can achieve good energy efficiency at the same brightness.
From the panel practitioners' analysis, we know that Sande's QD-OLED panel is similar to the traditional W white OLED + color RGB OLED TV panel in terms of material cost, and the material cost is actually more economical when the material process is mature.
But because the traditional W white OLED + color RGBOLED TV panel yield rate has reached more than 95%, so it is believed that the current QD-OLED panel cost of Samsung Display is at least 1.3~1.5 times of the traditional W white OLED + color RGBOLED TV panel, Samsung Display can only increase the selling price in the market to make up for the lack of yield in order to reduce the loss The resulting cost increase.
So far in two models of electricity - Samsung S95B and Sony A95K, two sizes: 55-inch and 65-inch QD-OLED TV, Samsung S95B overseas selling price of about 20,000 yuan, while the domestic listing of Sony A95K price is 27,000 yuan, is about five times the same period LCD TV, while the same period The LGD55 inch OLED TV, the price is only $7,399 after the dealer discount, before the discount is about 10,000 yuan. In addition, the domestic use of LGD55 inch OLED panel of e-commerce brand TV, the price is less than 5,000 yuan, only a quarter of the Samsung QD-OLED TV.
This fully illustrates the Samsung QD-OLED products in addition to the panel cost factor, there are many supporting industry chain costs are still high, such as driver chips, picture quality engine algorithms and so on.
In fact, Apple's display team has also evaluated Samsung's QD-OLED panel, but still has not found a suitable algorithm to match Apple's current image matrix, which shows that there is still a lot of room for progress in QD-OLED's color tuning.
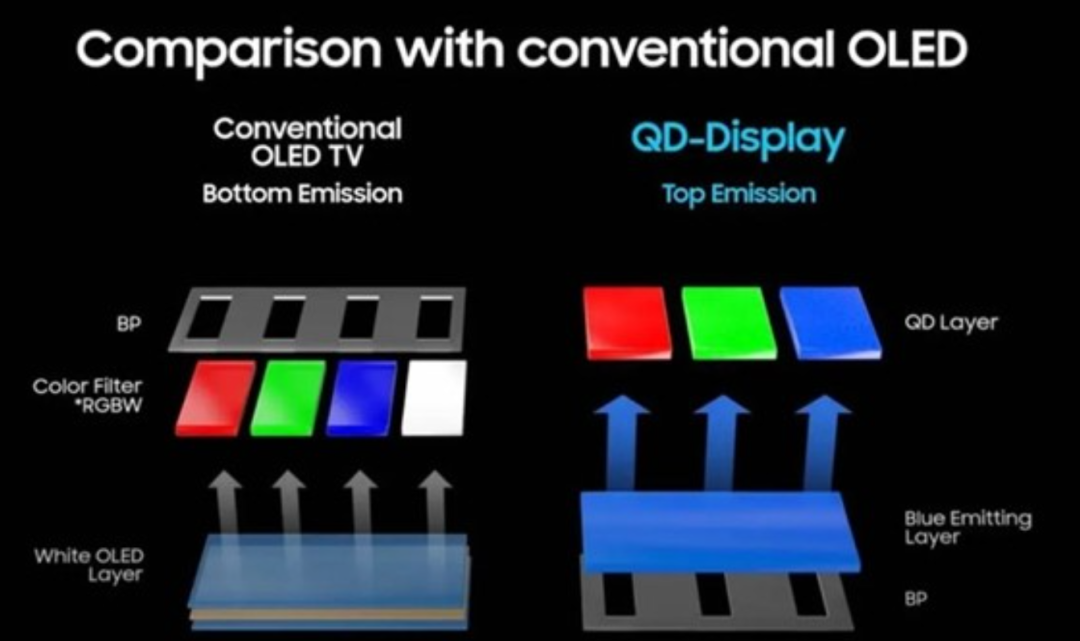
The face of large OLED panel market, mainland China panel makers in addition to Huike had hinted at replicating LGD's W white OLED + color RGBOLED panel process route in Changsha, in addition there is mention to invest in OLED TV panels of the two panel giants BOE and TCL Huaxing, both said more interested in investing in printed OLED TV panel capacity.
BOE and TCL Huaxing has been exhibiting their respective printed OLED TV panel products for many years, and the capital side of mainland China also put the main mass production of printed OLED equipment of the U.S. companies for shareholding cooperation to ensure that more original technology can be validated and landed in mainland China.
But according to the news coming out of the supply chain, the current printed OLED technology in mainland China, although there are several R & D platforms have from time to time related technology breakthroughs, but in the printed OLED light-emitting materials research and development, mass production process environment development and other key aspects, still have not obtained a stable parameter data model, still can not do mass production process package packaging. So although the printed OLED has a theoretical low material cost advantage, in fact, for the time being, but can not achieve mass production certification.
And there is a Samsung display QD-OLED the same problem, that is, mainland China in the development of printed OLED panels for the drive chip progress is not satisfactory, in addition to the picture quality engine algorithm software development, but also no breakthrough progress.
Industry professionals said that the printed OLED light-emitting materials in research and development is actually not a big problem, but to maintain its stable performance in the mass production environment is not affected by ambient temperature, humidity, gas solvents, is the industry's biggest headache. And because the OLED light-emitting material formula patents are stuck in the hands of foreign counterparts, to optimize the process on the basis of its patent license is extremely difficult, in fact, if it can be optimized, foreign material giants have long wanted to actively industrialize it, because the stable OLED light-emitting material breakthroughs, is the key opportunity for the display panel industry to really appear in the market update iteration.
And to develop new OLED light-emitting materials at the existing OLED light-emitting material system, mainland China not only lacks a real accumulation of material models, and even some basic principles of research have not really been completed. If the materials industry in mainland China can really master the organic polymer energy level jump and photon scintillation, extractive extinction principle and mechanism, and put forward their own material system, then in fact, regardless of vapor deposition, sputtering, immersion plating or printing mass production process, can be achieved.
In the material system are not sound conditions, mainland China's printing OLED equipment manufacturing can not be finalized, mass production line can not be planned.
In fact, the industry said BOE may first invest in mainland China to build a high-generation OLEDIT TV panel production line, but the process and equipment still follow the current 6-generation AMOLED production line vapor deposition process.
recommend
Feb 03, 2024
Recently, overseas institutions have downgraded Apples rating. For a time, Apple from being bearish in mainland China du...
Hot