Recently, the industry chain news that Apple to Samsung Display and LGD's medium-sized AMOLED panel reference process package using a glass single substrate solution, neither the original flexible AMOLED structure, nor the industry's commonly used double glass plywood rigid AMOLED structure.
It is understood that Apple's AMOLED R & D team in South Korea has been developing a new medium-sized AMOLED panel, for the follow-up from ordinary video and audio real-time interaction, upgrade to live-action video interaction to prepare the hardware.
Live-action video interaction because of the need for strong depth-of-field location discrimination, Apple in addition to the pre-development of successful spatial audio technology, but also hope to achieve spatial video technology through display technology, the distant and near objects can be displayed clearly at the same time, but also reflect the true depth of field spatial sense, rather than using the current mode of background defocus, loss of real-world details to enhance the sense of space.
The existing AMOLED is a self-luminous display technology, and the main graphics processing technology is also RGB digital color mixing, so it can be digitally adjusted for each display pixel, and as long as the images of different depths of field in the filming equipment are fused, a real live-action video reproduction can be achieved.
In the AMOLED mass production process, in fact, the most original mass production process, is the single glass substrate process, only because of the early in dealing with AMOLED light-emitting layer sealing process, due to the lack of suitable packaging technology, so still use a similar LCD LCD panel of the double-glass ensemble process, in order to achieve easier mass production.
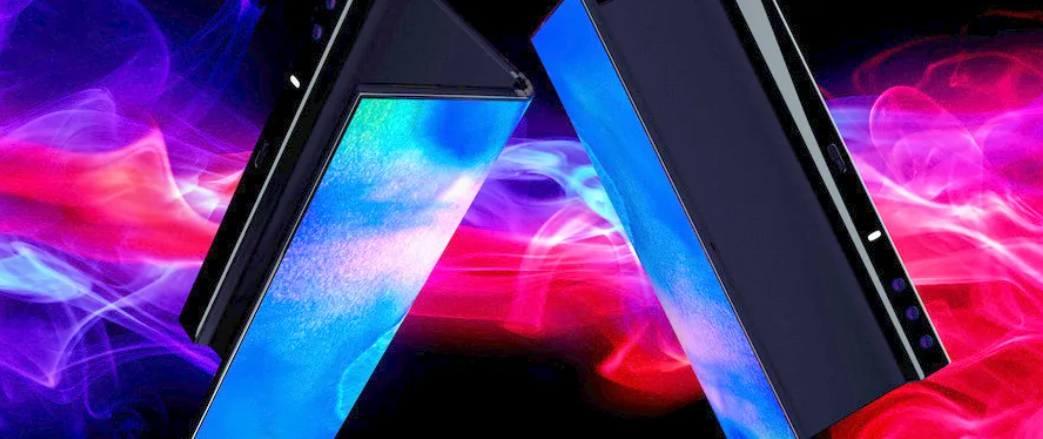
Later, as more and more semiconductor packaging process was introduced into the AMOELD packaging technology, inorganic material layer and organic special layer plus transparent PI layer of composite packaging technology, the perfect solution to the AMOLED luminous material isolation of water and oxygen pouring corrosion and ion, electron self-migration problems, coupled with laser peeling technology, you can start the PI layer of AMOLED panels, the complete AMOLED Panel stripped down, so there is a flexible AMOLED panel, that is, eliminating the original glass substrate "bulky", and can be attached to the "strength" of the better protective cover material, has become the mainstream technology of AMOLED panel mass production process.
However, flexible AMOELD panel is not a perfect display panel, especially in high-definition content display and live-action video display, because flexible AMOLED does not have a perfect "flat" display interface, so it will be very standard pointing to the live-action display content distortion, thus losing the meaning of high-definition display and live-action display Therefore, Apple has chosen a medium-sized display panel.
Therefore, Apple in the choice of medium-sized display panel, still choose the rigid package of glass substrate, but because the LCD LCD technology in the single-pixel contrast adjustment can not meet Apple's requirements, Apple still chose from the MEMS mechanical color mixing display and self-illumination display two path breakthrough.
Apple originally hoped that the MEMS mechanical toning display and MicroLED display technology, but in assessing its mass production, there is not so large semiconductor wafer production capacity to meet demand, thus turning again to the current life and luminous efficiency are poor AMOLED display technology.
In the process of Apple's development of new AMOLED panels, LGD provided Apple with its tandem OLED display technology developed for automotive displays, allowing the two industry challenges of lifetime and luminous efficiency to be effectively improved. In terms of mass production process technology, Samsung Display provided more mass production experience for Apple to study.
At the same time, Apple's AMOLED R&D team also reached a consensus with the glass substrate supplier, hoping that the glass substrate supplier would use many of the glass strengthening formulas and processes originally used in the protective cover glass, also used in the AMOLED substrate glass, so that Apple would save the material cost and processing process cost of re-laminating the protective cover glass for medium and large AMOLED displays.
In this way, Apple's medium-sized AMOLED panel mass production process, you can completely use the existing flexible AMOLED panel process, and also eliminates the laser peeling link, reducing the thermal modification of AMOLED light-emitting materials when the laser peel, you can use a lower temperature AMOLED light-emitting materials to achieve higher luminous efficiency and longer service life.
In fact AMOLED display technology there are many advantages can be tapped out, before Samsung there is an old man patting the R & D and mass production trial and error, but from 2014 onwards, the industry AMOLED mass production process breakthroughs, almost all from Apple's promotion.
The reason is simple, AMOLED companies do not have the courage to bear any "new process" brought about by the loss of production lines, especially in the "mature process" are difficult to make money in the case of profitability. Apple is different, it now has the financial ability to support the mass production process conversion costs, but also can define their own AMOLED panel display standards to reduce the cost of quality, so as to achieve their own "dedicated capacity breakthrough".
Apple let AMOLED mass production process back to the initial single glass stack state, seemingly "rigid and flexible" behind, in fact, is still on the glass substrate line technology-based traditional flat panel display technology mass production process has a more profound understanding, from the root to remove the "fancy "After the patch process, also let the flat panel display mass production technology back to the "right track".
Our Authors
We have experienced employees who choose the services we provide, and our services are all professional. If you contact us, we may receive a commission.
Why You Can Trust ELECTREND
15
Years of service experience
580+
Brand Customer Choice
1000+
The choice of corporate customers